Quality
In the customer driven business environment, it is well known that “Quality” is the determining factor for success. To provide continuously improved services to the customer, NSH has established a quality system covering all of its functions. It has been qualified & certified for ISO 9001 Standard by TUV NORD Germany.
The management of NSH is committed to the best quality of services to the customers and to achieve leadership among the competitors. Understanding the vital role of quality system, the top executive management is directly involved in the monitoring & reviewing of the quality system. Selected personnel from various disciplines have been assigned to enforce the quality systems & to provide training to all employees.
Quality system documents have been grouped into four levels named Quality system manual (level-1), procedures (level-2), work instructions & specifications (level-3) and formats & records (level-4). Distribution & Control is emphasized through document controllers both at corporate level and at sites.
Quality plans are prepared based on the client’s specifications & standards and distributed to the sites. Inspection & testing are performed at three stages named receiving, in process & handing over stages. Calibration of instruments & gauges is ensured prior to its usage. Defective materials & non-conforming works shall be identified, recorded, reviewed & resolved accordingly. Applicable Quality control records are maintained till the final completion of the project & submitted to the client as per respective ITP.
Audits are carried out at corporate & site level by trained & qualified auditors at predetermined intervals. Results of the audits shall be recorded & reviewed by the management review committee. Corrective actions shall be decided in the meeting & implemented. Its effectiveness shall be monitored by identified personnel.
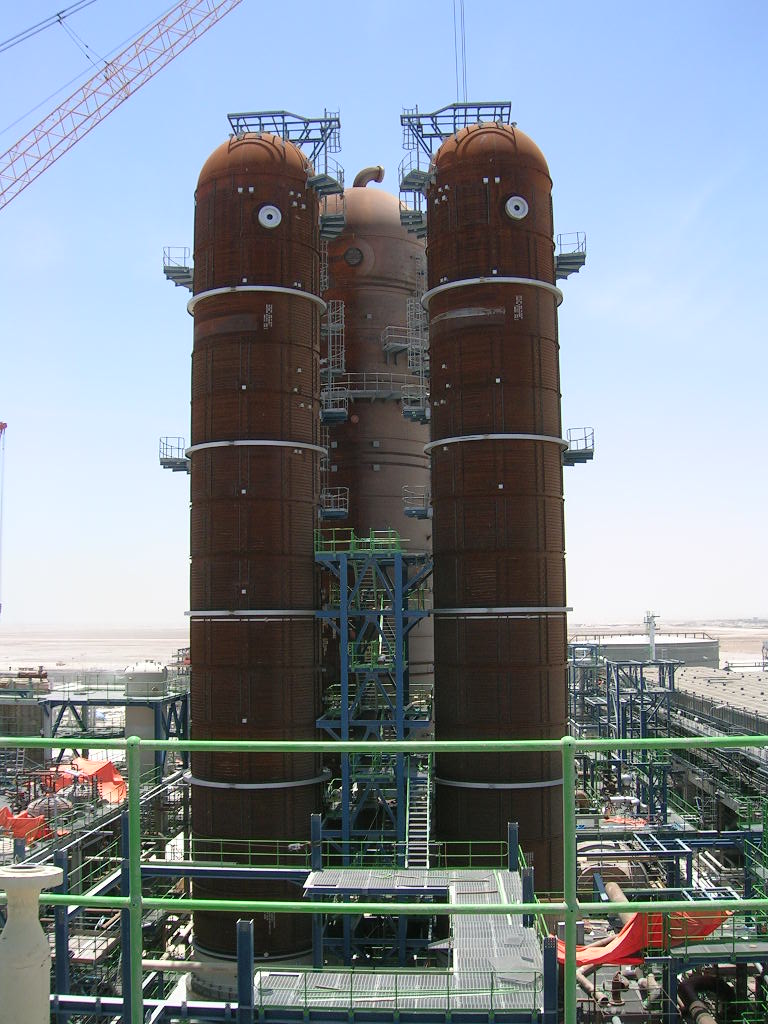